Product overview
Nail polish has been developed to have a faster drying time with brands claiming "dry in 60 seconds" or "quick-dry". However, smudging a manicure is still a common complaint. There are also difficulties accelerating the drying time of more natural polishes containing fewer volatile solvents. This requires new products to be tested in a consistent and controlled way. A precise sample preparation method and a timed test sequence within Exponent Connect software was therefore developed to provide a solution to this assessment requirement and so that operators can perform testing with minimal operator intervention.
During the polish drying time test, a channel 20cm long is filled with polish to a depth of 0.5 mm and wiped level using a glass rod. At this point a timer within the software test sequence is started. This depth is representative of a typical coat of polish on a fingernail; a depth of 0.5mm dries to approximately 0.2mm. This channel is seated on top of the Adhesive Indexing System that has ten detents and so ten test sites are available by simply sliding the platform along. A 1" Indexable Ball Probe is used for the tests, which can be rotated to allow a clean test site without replacing the probe or the requirement to clean and dry the test probe between tests. This is used to perform an adhesive test at the first test site. A force of 750g is held for 5 seconds to allow a bond to form. The probe is then quickly withdrawn, breaking the nail polish bonds and the force to do this is measured. The channel is moved along to the next site and the test repeated. A set of ten tests are performed in this way with pre-set time delays between the tests. Tests are performed over the whole drying period of the polish.
Several measurements can be made from the force-time graph:
- The maximum force needed to withdraw the probe from the sample is a measure of the strength of the bond or the adhesiveness of the polish. The initial wet polish has a very low adhesive force. As time passes the stickiness increases until it peaks, then drops off. The polish has been found to be touch dry after the peak.
- Similarly, the work of adhesion is the total energy required to pull the probe from the polish each time and is represented by the area under the force-distance graph for each test cycle.
- Softness is defined as the distance the probe is required to sink into the surface of the polish before the force reaches 25g. The softness decreases with drying time until it reaches a plateau, at which point the polish is touch dry.
- Stringiness is the distance the probe withdraws while the polish is still adhered.
The series of adhesion tests is automated by a unique test sequence developed in Exponent Connect software, with parameters such as the delay between tests, the number of repeats, applied force and holding time adjusted by the user if necessary. Additionally, an analysis macro is available to measure the above four properties across all repeats at the press of a button. With the addition of instruction messages in the sequence this provides a user-friendly solution for this type of product testing.
This rig requires attachment to an Adhesive Indexing System (A/90PR) and would also be suited to the testing of liquid adhesives or samples that have a curing process.
How does the Nail Polish Adhesion Rig work?
Typical graph
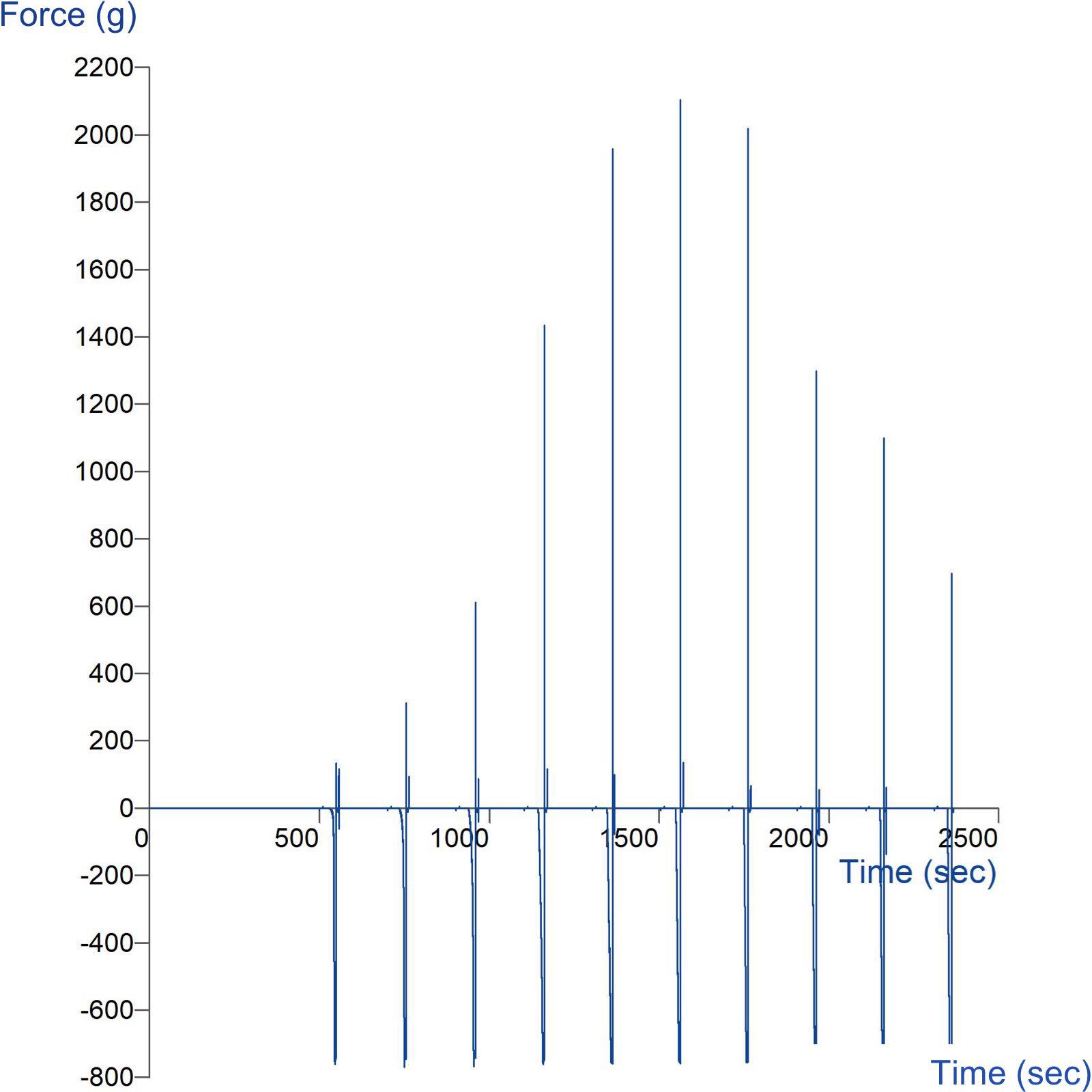
Technical information
Ideal sample form
Samples that can be formed into the channel to a fixed thickness.
Benefits and limitations
- Multiple testing provided from a single sample preparation.
- Samples can be formed to a fixed depth/thickness.
Installation
Full installation instructions are provided within the Education Zone of the latest Exponent/Connect software version and on the technical information sheet accompanying this product.
Chemical compatibility
Stable Micro Systems probes and attachments are commonly made from four materials: anodised aluminium (AA6082 T6), stainless steel (316 T), Delrin (acetyl copolymer) and Perspex (polycarbonate).
In general use, probes and attachments made from these materials will be suitable for testing food products and inert non-food materials.
The four materials listed above are not universally resistant to all types of chemicals and as such the compatibility of the probe/attachment material with the product (to be tested) must be established to prevent damage to the probes and attachments. If the compatibility of the product with the probe is unknown to the customer then the chemical information about the product (Material Safety Data Sheet or Product Data Sheet) should be submitted to Stable Micro Systems. Stable Micro Systems will then assess the suitability of the probe/attachment material for use with the product and advise accordingly. If this advice is not sought then Stable Micro Systems will not accept liability for probes/attachments damaged by chemical attack from the product being tested.
Cleaning and maintenance
All probes and attachments may be cleaned in warm (or hand hot) water using a mild detergent. A soft brush may be used but abrasive cleaning aids should be avoided. Stable Micro Systems products should not be microwaved or cleaned in a dishwasher.
Screw threads should be lightly lubricated after drying using a light lubricant, e.g. petroleum jelly, mineral oil. This will aid the fitting and unscrewing of the item. Each component of a probe or attachment should be wrapped separately when stored, to avoid scratching or chipping. This will safeguard against any unnecessary damage to the accessory.