Product overview
Extrudability is the work required to push or force out (or expel) a product. For products in tubes, such as syrups and icings, removal of the contents relies upon the consumer squeezing the packaging to extrude the product. The ability to squeeze the product out effectively is essential and the consistency of the contents of a tube or sachet is therefore fundamental to its ease of removal from the packaging when required. If the substance is too dense, consumers will experience difficulty extracting it; if it is too fluid, the product could leak. Assuming the orifice size remains constant, the force to squeeze the packaging depends largely on the consistency of the e.g. paste/cream
To attempt to mimic this situation a forward extrusion test can be employed. A Forward Extrusion Rig measures the compression force required for a piston disc to extrude a product through a standard size outlet in the base of the sample container. The base of the container accommodates a disc containing a central hole (termed the annulus) of varying diameter (3, 5, 7 or 10mm), depending upon the consistency of the sample. The complete sample container is located into a centralising insert fitted into the Heavy Duty Platform and a piston disc is attached to the load cell using a probe adapter which acts almost like a piston to compress the sample and causes forward flow through the annulus of the disc.
Products suitable for this type of test include pastes and viscous liquids without the presence of particulates.
How does the Forward Extrusion Rig work?
Typical graph
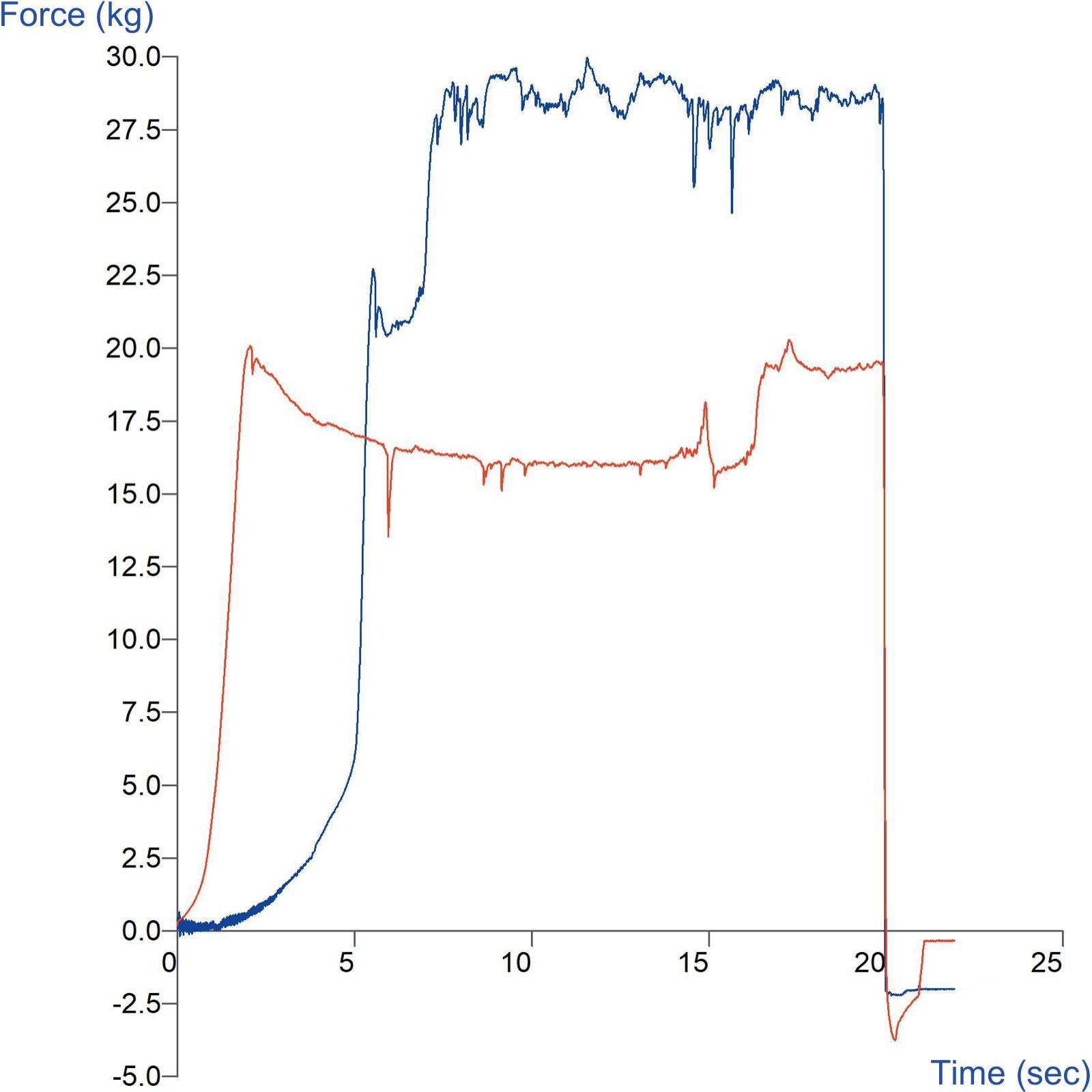
Technical information
Ideal sample form
Homogeneous viscous liquid and semi-solid materials which need to be contained in order to measure their extrusion properties by pushing through an orifice.
Benefits and limitations
- Provides an imitative test of real-life consumer situations
- Samples should not contain large air bubbles or particulates
Optional extras
Forward extrusion piston disc – HDP/FE-D
Insert with 3mm Ø outlet (pack of 3) – HDP/FE-BI3
Insert with 5mm Ø outlet (pack of 3) – HDP/FE-BI5
Insert with 7mm Ø outlet (pack of 3) – HDP/FE-BI7
Insert with 10mm Ø outlet (pack of 3) – HDP/FE-BI10
A Product Catchment Drawer (HDP/CAT) is recommended for collection of extruded sample under the Heavy Duty Platform during a test.
Installation
Full installation instructions are provided within the Education Zone of the latest Exponent/Connect software version and on the technical information sheet accompanying this product.
Chemical compatibility
Stable Micro Systems probes and attachments are commonly made from four materials: anodised aluminium (AA6082 T6), stainless steel (316 T), Delrin (acetyl copolymer) and Perspex (polycarbonate).
In general use, probes and attachments made from these materials will be suitable for testing food products and inert non-food materials.
The four materials listed above are not universally resistant to all types of chemicals and as such the compatibility of the probe/attachment material with the product (to be tested) must be established to prevent damage to the probes and attachments. If the compatibility of the product with the probe is unknown to the customer then the chemical information about the product (Material Safety Data Sheet or Product Data Sheet) should be submitted to Stable Micro Systems. Stable Micro Systems will then assess the suitability of the probe/attachment material for use with the product and advise accordingly. If this advice is not sought then Stable Micro Systems will not accept liability for probes/attachments damaged by chemical attack from the product being tested.
Cleaning and maintenance
All probes and attachments may be cleaned in warm (or hand hot) water using a mild detergent. A soft brush may be used but abrasive cleaning aids should be avoided. Stable Micro Systems products should not be microwaved or cleaned in a dishwasher.
Screw threads should be lightly lubricated after drying using a light lubricant, e.g. petroleum jelly, mineral oil. This will aid the fitting and unscrewing of the item. Each component of a probe or attachment should be wrapped separately when stored, to avoid scratching or chipping. This will safeguard against any unnecessary damage to the accessory.
Troubleshooting
Tape should be placed on the extrusion disk hole if a low viscosity sample is contained.
Friction between the extrusion disk and cell wall should be almost negligible. A ‘blank’ test should be performed to check this.