Product overview
The measurement of friction is important across a wide range of industries and applications, as friction is a fundamental force that influences the behaviour of materials, machines, and products. Understanding and quantifying friction is essential for, for example, material selection as different or new materials exhibit varying levels of friction when in contact with one another or for the assessment of surface treatment and coatings as these can alter the friction characteristics of materials. Measuring friction also aids in optimising the performance of materials for specific applications, considering factors like wear resistance, durability and lubrication requirements.
This attachment is used to determine the static and dynamic coefficient of friction for plastic film and packaging materials. It meets the requirements of ASTM-D 1894-90 and ISO 8295. It can be used to determine the friction characteristics of material sliding over itself as a reference material or other substances under specified test conditions.
The reference material is fixed firmly to the base and the test material to the sled. This sled is 63.5 x 63.5mm and weighs 200 +/-5g. The sled is pulled across the reference material at a constant speed and the force measured. The co-efficient of friction is determined from these results.
Typical graph
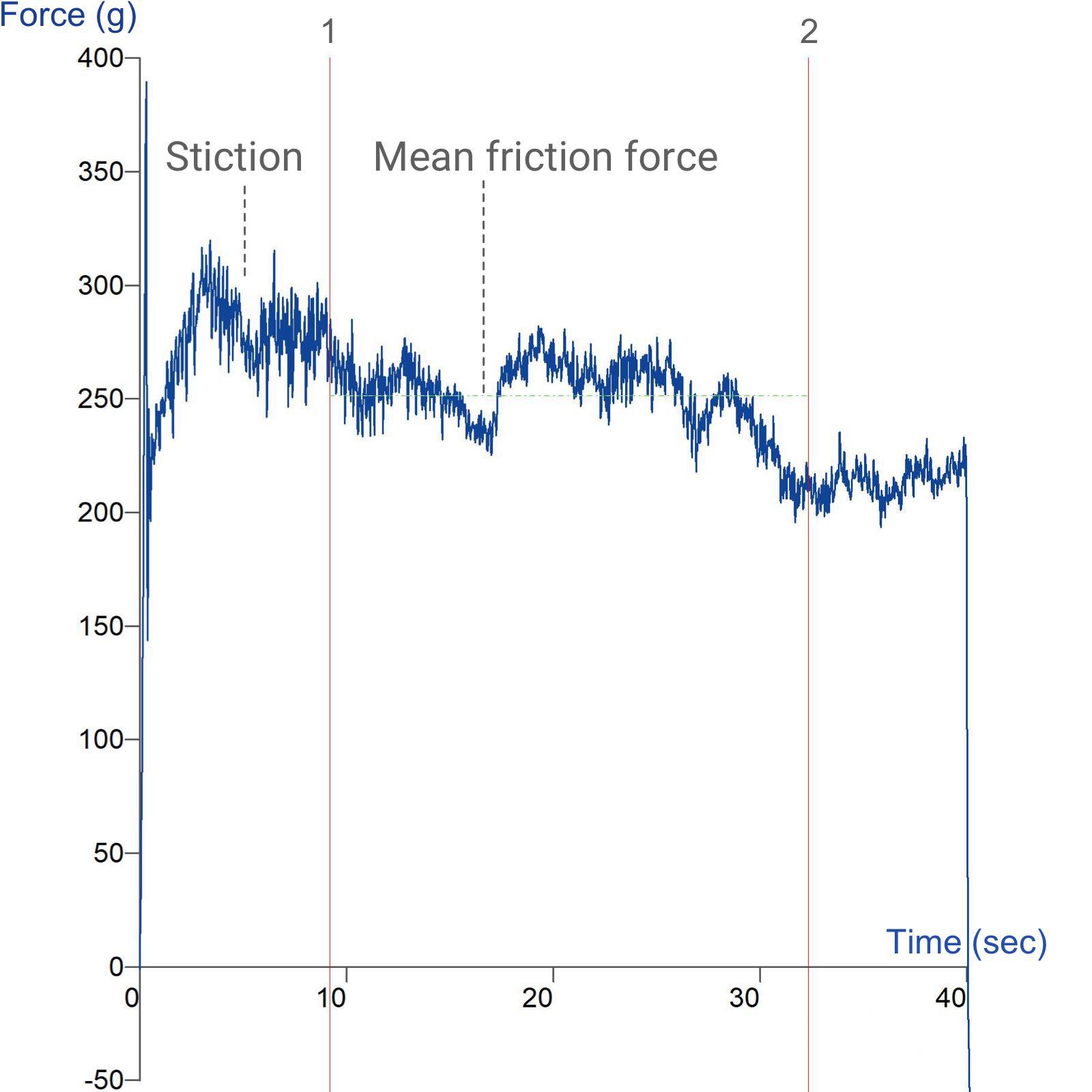
Technical information
Ideal sample form
Moderately thin layers of sheeted material, granules or creams.
Benefits and limitations
- Friction measurement is limited to one direction and is not cyclic
Installation
Full installation instructions are provided within the Education Zone of the latest Exponent/Connect software version and on the technical information sheet accompanying this product.
Chemical compatibility
Stable Micro Systems probes and attachments are commonly made from four materials: anodised aluminium (AA6082 T6), stainless steel (316 T), Delrin (acetyl copolymer) and Perspex (polycarbonate).
In general use, probes and attachments made from these materials will be suitable for testing food products and inert non-food materials.
The four materials listed above are not universally resistant to all types of chemicals and as such the compatibility of the probe/attachment material with the product (to be tested) must be established to prevent damage to the probes and attachments. If the compatibility of the product with the probe is unknown to the customer then the chemical information about the product (Material Safety Data Sheet or Product Data Sheet) should be submitted to Stable Micro Systems. Stable Micro Systems will then assess the suitability of the probe/attachment material for use with the product and advise accordingly. If this advice is not sought then Stable Micro Systems will not accept liability for probes/attachments damaged by chemical attack from the product being tested.
Cleaning and maintenance
All probes and attachments may be cleaned in warm (or hand hot) water using a mild detergent. A soft brush may be used but abrasive cleaning aids should be avoided. Stable Micro Systems products should not be microwaved or cleaned in a dishwasher.
Screw threads should be lightly lubricated after drying using a light lubricant, e.g. petroleum jelly, mineral oil. This will aid the fitting and unscrewing of the item. Each component of a probe or attachment should be wrapped separately when stored, to avoid scratching or chipping. This will safeguard against any unnecessary damage to the accessory.