Product overview
It is well known that conditioning shampoos and hair conditioners are used to provide a variety of benefits to hair: they reduce the combing force, enhance the gloss, confer smoothness and antistatic properties and they improve the manageability of the hair. Various types of benefit agents including cationic surfactants, polymers, emollients, and special compounds such as vitamins, UV filters, etc. contribute to cosmetic properties. For example, silicones are insoluble oils that are commonly used as conditioning agents for hair as they can effectively reduce combing friction of hair and provide a soft, smooth feel and a shiny appearance.
One of the methods that are used to determine conditioning efficiency is combability. Wet combability is measured under controlled conditions using an objective method in which a Texture Analyser measures the combing force required to pull a wet hair swatch (or tress) through a comb using the Hair Combing Rig. It is usually necessary to first detangle and then to tangle hair in a controlled and reproducible way before the measurements. Blank hair swatches containing only water are run through the test to establish an initial benchmark. Then, the test solution is applied to the same swatch and measured for combability again to determine if, for example, the conditioner provides any improvements in combing. The maximum force to comb and the total work done are taken as comparative measures. A reduced combing force and work (usually calculated in percentage terms of a treated hair tress compared to the same tress treated with a blank formulation, i.e. no polymer) implies easier wet combability associated with the removal of entanglements of the hair fibres and can therefore be used to substantiate claims of improved manageability.
The combing force evaluation is equally effective for assessing combability of dry hair. All modified hair types (e.g. chemically treated (bleached), delipidised (by solvent extraction), and polymer treated hair) show an increase in dry combing forces as quantified by combing measurements. The combing work (g cm) and force as a function of tress distance would be substantially higher for all modified hair types compared to that of virgin hair and therefore this method can be used to assess, for example, the effect of addition of smoothing serums to dry hair.
When assessing combability, a researcher may typically need to perform the comb force test for a certain number of combing cycles in order to obtain a complete assessment of the effects of a treatment with repeated combing. The Hair Combing Rig comprises a unique mechanical function that allows ‘before and after’ tests in continuous combing strokes in order to replicate consumer action. The rig is positioned on the Texture Analyser and the supported length of hair is held vertically, near to the comb. When instructed, the arm of the Texture Analyser brings the comb down through the hair, recording the necessary force as it moves. At the end of a stroke, the comb is mechanically disengaged and moves back to its starting position to begin the next combing cycle. This can be continued for as many cycles as is required within one test to complete the assessment.
This multi-cycling capability is unique to Stable Micro Systems Hair Combing Rig design compared to the limited single cycle testing of alternative equipment.
Either 1 x 4 row combs (A/HCR/SC) or Comb clamp (A/HCR/CG) are required to complete the device for testing.
How does the Hair Combing Rig work?
Typical graph
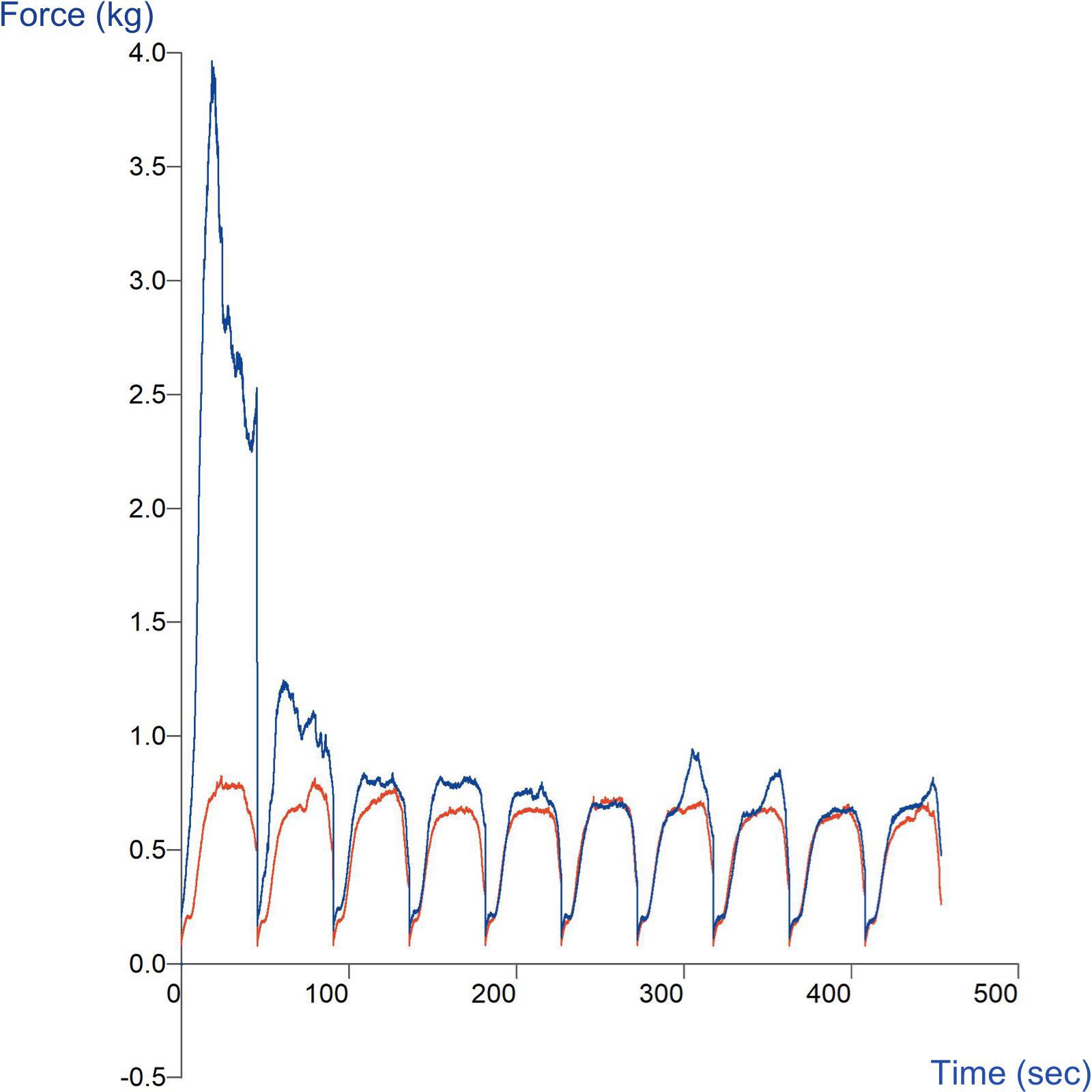
Technical information
Ideal sample form
Hair tresses that can be clamped in order to comb.
Benefits and limitations
- Multiple cycle testing provides a continuous combing action for a chosen number of cycles which is limited to one cycle in most other testing alternatives.
- The hair tress length needs to be optimised within the height of this rig to provide combing to the end of the tress.
Optional extras
Adapter to fit A/HCR to TA.HDPlusC Texture Analyser – A/HCR/ADHD
Installation
Full installation instructions are provided within the Education Zone of the latest Exponent/Connect software version and on the technical information sheet accompanying this product.
Chemical compatibility
Stable Micro Systems probes and attachments are commonly made from four materials: anodised aluminium (AA6082 T6), stainless steel (316 T), Delrin (acetyl copolymer) and Perspex (polycarbonate).
In general use, probes and attachments made from these materials will be suitable for testing food products and inert non-food materials.
The four materials listed above are not universally resistant to all types of chemicals and as such the compatibility of the probe/attachment material with the product (to be tested) must be established to prevent damage to the probes and attachments. If the compatibility of the product with the probe is unknown to the customer then the chemical information about the product (Material Safety Data Sheet or Product Data Sheet) should be submitted to Stable Micro Systems. Stable Micro Systems will then assess the suitability of the probe/attachment material for use with the product and advise accordingly. If this advice is not sought then Stable Micro Systems will not accept liability for probes/attachments damaged by chemical attack from the product being tested.
Cleaning and maintenance
All probes and attachments may be cleaned in warm (or hand hot) water using a mild detergent. A soft brush may be used but abrasive cleaning aids should be avoided. Stable Micro Systems products should not be microwaved or cleaned in a dishwasher.
Screw threads should be lightly lubricated after drying using a light lubricant, e.g. petroleum jelly, mineral oil. This will aid the fitting and unscrewing of the item. Each component of a probe or attachment should be wrapped separately when stored, to avoid scratching or chipping. This will safeguard against any unnecessary damage to the accessory.