Product overview
Many years ago, two variants of Powder Compaction Rig (high tolerance and low tolerance) suited to high force applications were introduced. There is however a need for powder compaction testing of similar sample volumes at lower compaction forces than the existing methods that require a TA.HDplusC Texture Analyser. As such we developed two low force powder compaction attachments that provide indexable testing of 10 samples up to 50kg (A/IPC0.5) and 10kg (A/IPC5) which also serve to increase useability and efficiency. Once the first sample is centralised with the testing probe, subsequent samples can simply be moved along via a 'quick-click' mechanism which aligns the next test ready to go, therefore increasing sample throughput.
Compaction properties of powders can be assessed using target force or target distance modes. Many powder compacts are formed to a target distance and so the Powder Compaction Rigs can be used to assess required force. New advances in tabletting machines allow compression to a target force resulting in powder compacts with constant porosity. The Powder Compaction Rig can be used with target force mode to assess the effect of fill level/weight on tablet thickness. In addition, by looking at the loading, hold, and unloading periods of a hold until time graph the information on compressibility, relaxation, stiffness and elastic recovery can be calculated.
How does the Indexable Powder Compaction Rig work?
Typical graph
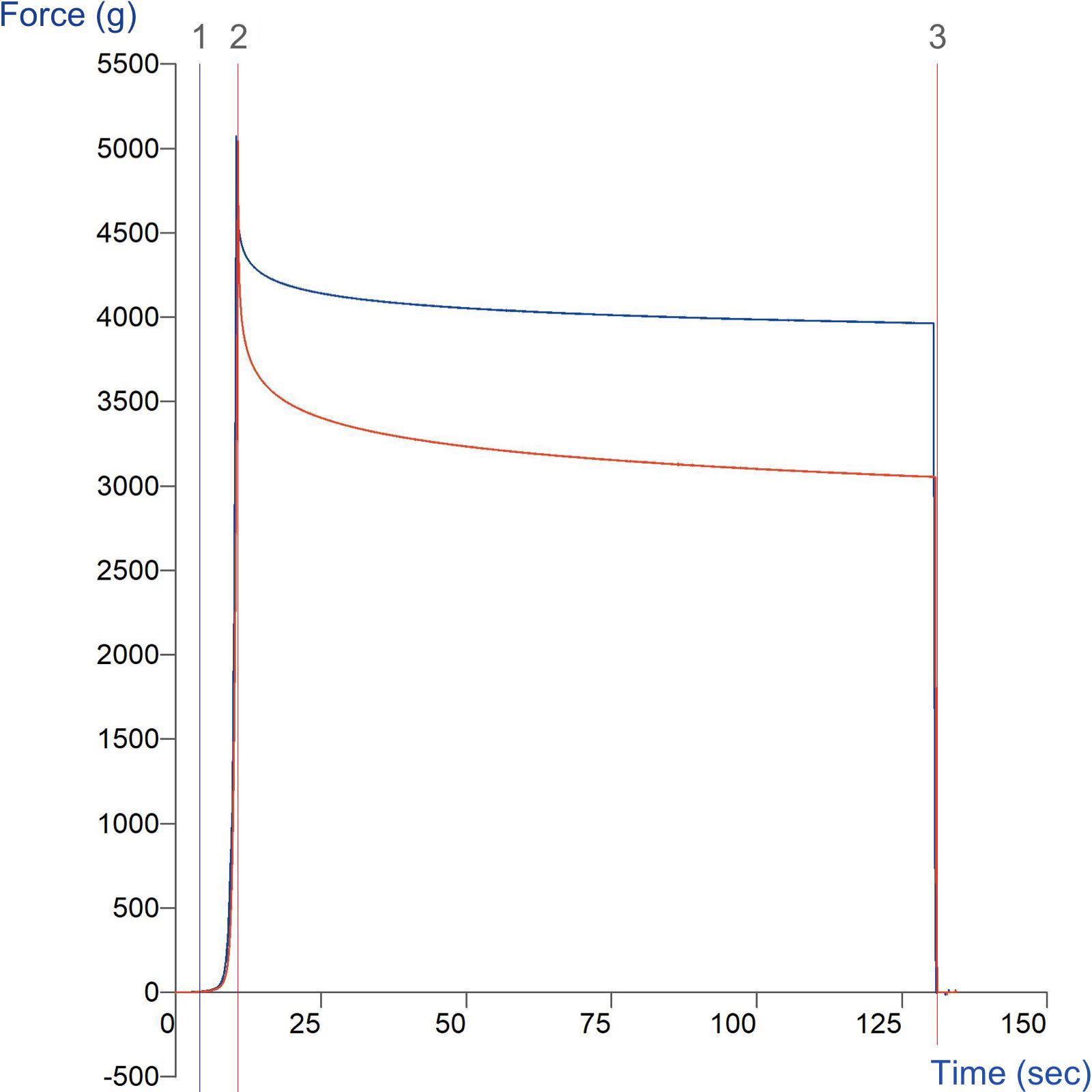
Technical information
Ideal sample form
Powdered/granular material.
Benefits and limitations
- Allows a simple test to be performed with increased efficiency.
- Small sample size.
Installation
Full installation instructions are provided within the Education Zone of the latest Exponent/Connect software version and on the technical information sheet accompanying this product.
Chemical compatibility
Stable Micro Systems probes and attachments are commonly made from four materials: anodised aluminium (AA6082 T6), stainless steel (316 T), Delrin (acetyl copolymer) and Perspex (polycarbonate).
In general use, probes and attachments made from these materials will be suitable for testing food products and inert non-food materials.
The four materials listed above are not universally resistant to all types of chemicals and as such the compatibility of the probe/attachment material with the product (to be tested) must be established to prevent damage to the probes and attachments. If the compatibility of the product with the probe is unknown to the customer then the chemical information about the product (Material Safety Data Sheet or Product Data Sheet) should be submitted to Stable Micro Systems. Stable Micro Systems will then assess the suitability of the probe/attachment material for use with the product and advise accordingly. If this advice is not sought then Stable Micro Systems will not accept liability for probes/attachments damaged by chemical attack from the product being tested.
Cleaning and maintenance
All probes and attachments may be cleaned in warm (or hand hot) water using a mild detergent. A soft brush may be used but abrasive cleaning aids should be avoided. Stable Micro Systems products should not be microwaved or cleaned in a dishwasher.
Screw threads should be lightly lubricated after drying using a light lubricant, e.g. petroleum jelly, mineral oil. This will aid the fitting and unscrewing of the item. Each component of a probe or attachment should be wrapped separately when stored, to avoid scratching or chipping. This will safeguard against any unnecessary damage to the accessory.