Product overview
For products with variable texture across their length, e.g. cereal bars, results from single blade tests may be highly variable. This is because for one blade test of a cereal bar the blade may come into contact with e.g. a peanut and a chocolate chip, and the next blade test of the same bar may slice through a raisin and an apricot piece, thus the blade is almost testing different samples. The multiple blades of a Kramer Shear Cell provide a measurement on several positions at the same time thus local texture deviations are compensated for with this method which provides an averaging effect and has shown to be more reproducible for highly variable samples.
The Kramer Shear Cell can be used for multi-particle products such as cereals and pickles in sauce together with fruit and vegetables such as peas and beans. For self-supporting samples, such as cereal bars or meat blocks/slabs, testing can be simplified by the use of the multi-blade head of the Kramer Shear Cell without the need to contain the sample in the cell and testing performed directly on a flat testing platform.
This test bulk testing method incorporates the principles of compression, shearing and extrusion. The Kramer Shear Cell uses a stationary rectangular box with slots in the bottom to hold the sample and a moving probe composed of 5 or 10 blades to drive through the test specimen. Pieces are placed into the cell to the same filling volume or by weight, and the blades positioned at a constant position above the sample surface. The blades then move down into the sample compression, shearing and extruding the bulk to a point close to, or slightly through, the base of the cell. Because individual multi-particle products can be tested, the apparatus permits the determination of the distribution pattern, as well as of an average resistance for a lot of the test material. Both maximum force readings and areas under the peak (work function) can be determined.
The A/KS5 is fitted with 5 blades and can be used for lower force applications but a 50kg Load Cell or greater is still recommended. The A/KS10 Kramer Shear Cell is fitted with 10 blades and is used when the applied load is greater than 50kg.
Easy locating adapters are provided which facilitate fast blade removal for cleaning and replacement or further testing. Both cells have perspex front panels which provide easy visual positioning of the blades close to the sample.
How does the 5 Bladed Kramer Shear Cell work?
Typical graph
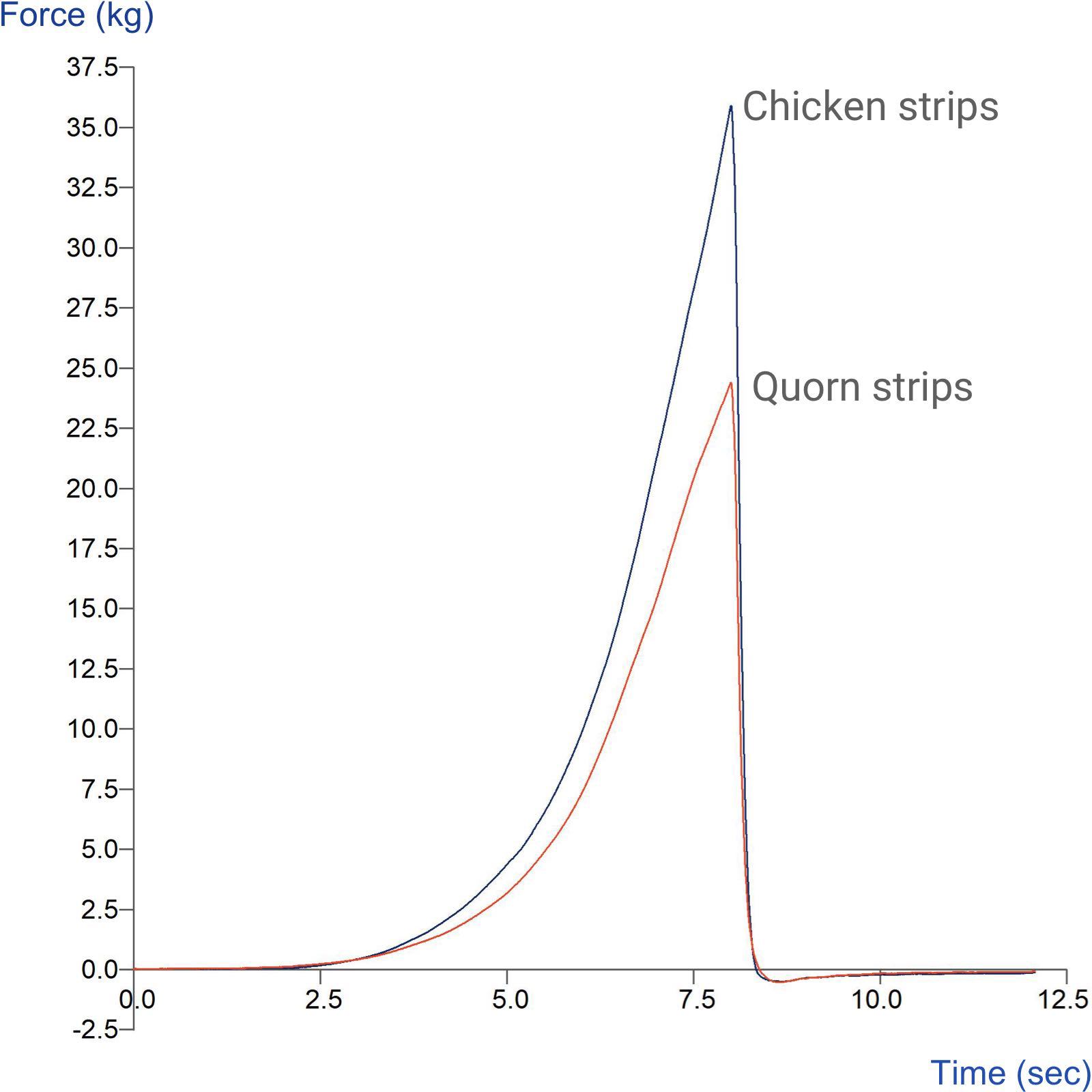
Technical information
Ideal sample form
This attachment can be used to cut through a sample which is solid and self-supporting (by using the upper blade head on its own) or a sample which needs to be contained (usually for the reason that the sample consists of small irregular pieces which cannot be successfully tested on their own). If you consider that if the upper set of teeth were straightened they would effectively form a knife edge – using any form of blade can therefore represent the force to cut or 'bite' into a sample. This device consists of 5 or 10 blades mounted together to create an averaging effect when is required for the testing of a sample which is non-homogeneous or multi-particulate.
Benefits and limitations
- An averaging effect is created from this measurement where samples cannot be repeatably tested in individual pieces.
- Self-supporting materials can be tested using the blade head only which may make test setup and cleaning between testing easier.
- This test may require a twin column Texture Analyser due to its high force requirement.
Optional extras
A Product Catchment Drawer (A/CAT) is recommended for collection of extruded sample under the attachment during a test.
Installation
Full installation instructions are provided within the Education Zone of the latest Exponent/Connect software version and on the technical information sheet accompanying this product.
Chemical compatibility
Stable Micro Systems probes and attachments are commonly made from four materials: anodised aluminium (AA6082 T6), stainless steel (316 T), Delrin (acetyl copolymer) and Perspex (polycarbonate).
In general use, probes and attachments made from these materials will be suitable for testing food products and inert non-food materials.
The four materials listed above are not universally resistant to all types of chemicals and as such the compatibility of the probe/attachment material with the product (to be tested) must be established to prevent damage to the probes and attachments. If the compatibility of the product with the probe is unknown to the customer then the chemical information about the product (Material Safety Data Sheet or Product Data Sheet) should be submitted to Stable Micro Systems. Stable Micro Systems will then assess the suitability of the probe/attachment material for use with the product and advise accordingly. If this advice is not sought then Stable Micro Systems will not accept liability for probes/attachments damaged by chemical attack from the product being tested.
Cleaning and maintenance
All probes and attachments may be cleaned in warm (or hand hot) water using a mild detergent. A soft brush may be used but abrasive cleaning aids should be avoided. Stable Micro Systems products should not be microwaved or cleaned in a dishwasher.
Screw threads should be lightly lubricated after drying using a light lubricant, e.g. petroleum jelly, mineral oil. This will aid the fitting and unscrewing of the item. Each component of a probe or attachment should be wrapped separately when stored, to avoid scratching or chipping. This will safeguard against any unnecessary damage to the accessory.
Troubleshooting
Blades can be difficult to align in blade guides and slots. Check that friction is not being measured by performing a ‘Blank’ test using a Button Trigger.